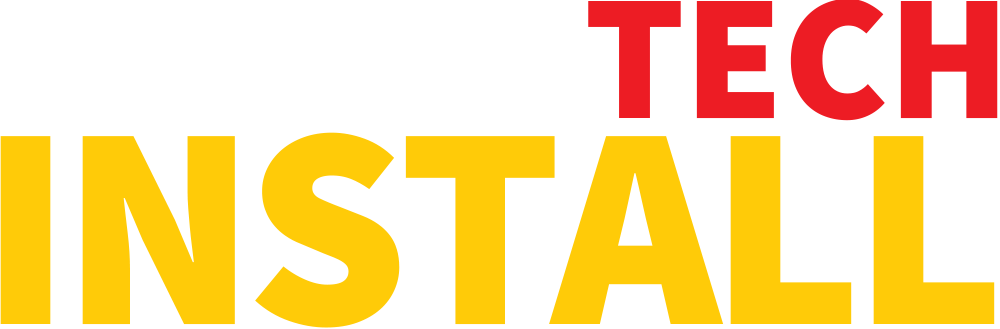
The quality ReadyLIFT kit integrates more than a simple lift or front leveling. It was created to meet the demand for a kit that leveled out the front end without sacrificing ride quality. Since the kit uses replacement coil springs as opposed to a spacer puck, the truck’s ride isn’t affected in any negative way. The installation of the lift kit was completed at PowerTech Diesel in Idaho Falls, Idaho, by technician Travis Prouse along with some help from techs Tyler Olsen and Jordan Johnson. The wheels and tires were sent off to another shop to be mounted and balanced before being installed on the truck.

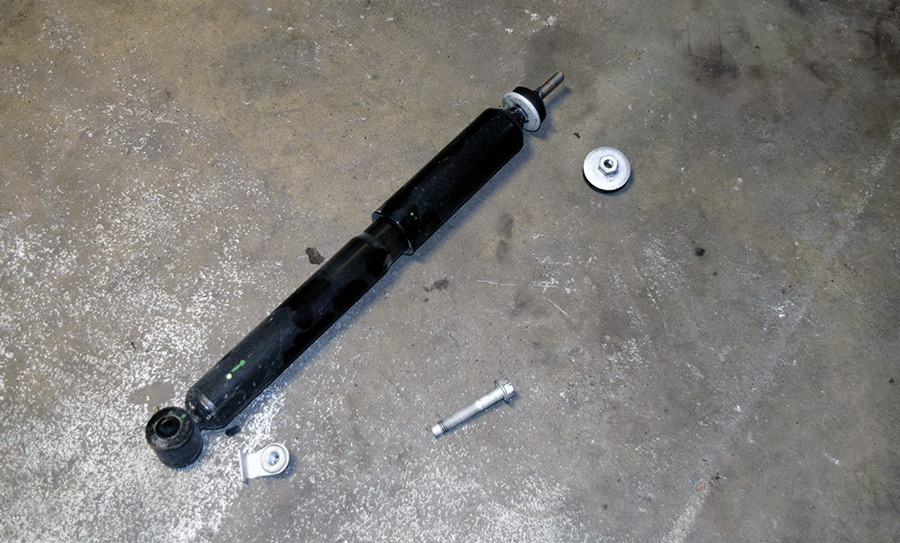
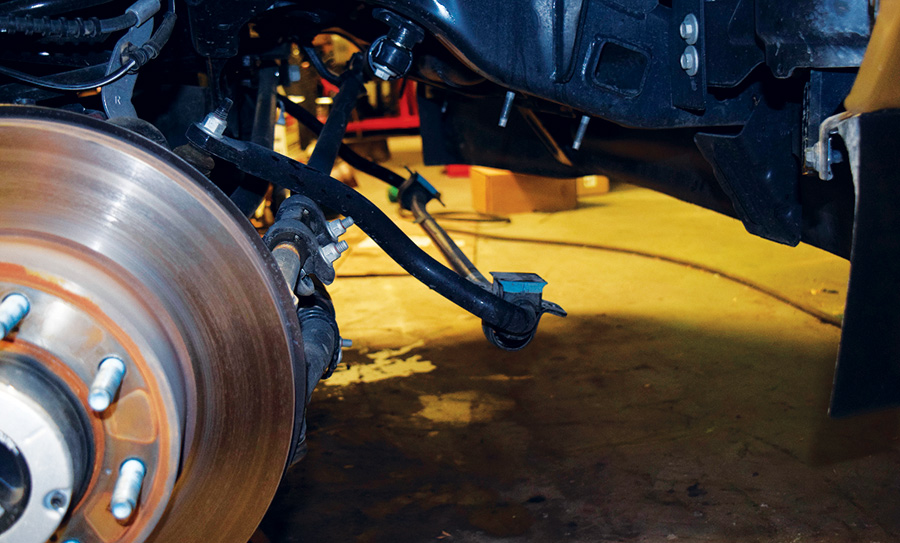
After playing with the lift a little, he was able to pull the shock out. He repeated the same process for the driver side. After that, he went on to unbolting the front sway bar brackets from the frame so he could get the sway bar out of the way in order to remove the springs. He subsequently removed the springs upon raising the truck, and then he put in the new springs with the existing rubber buffers from the old ones.
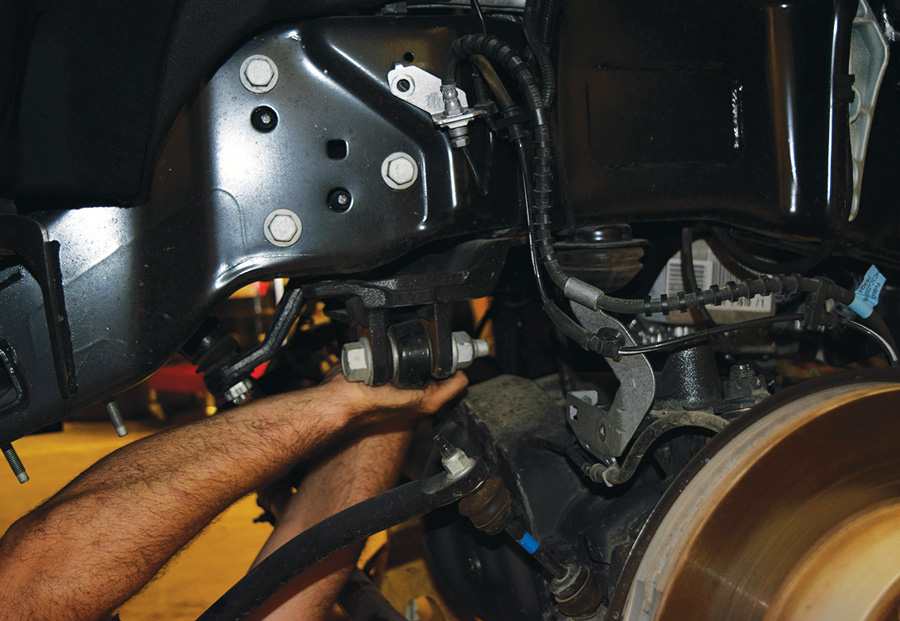
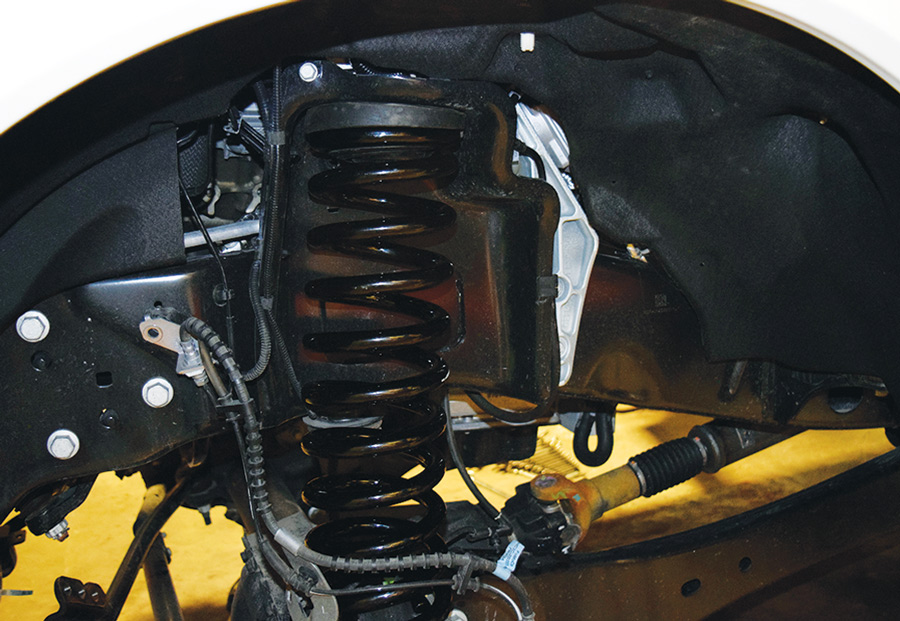
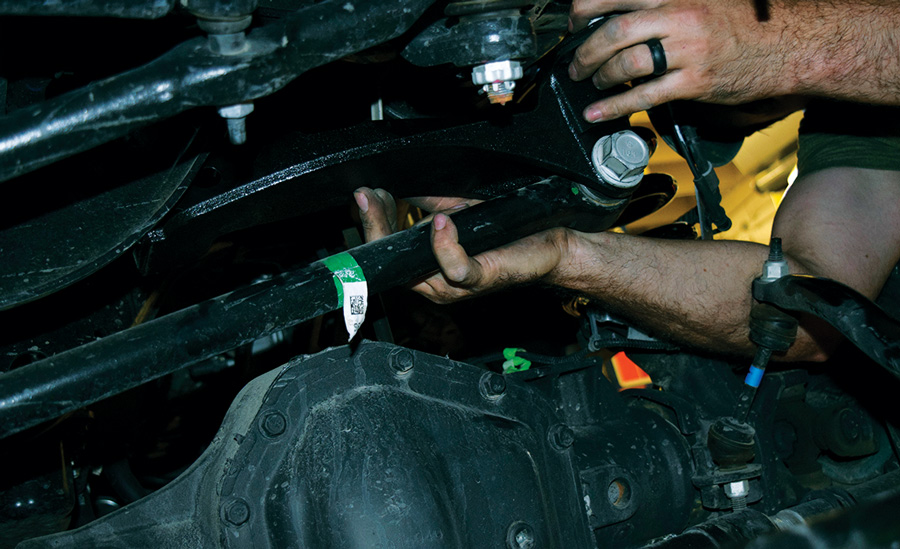
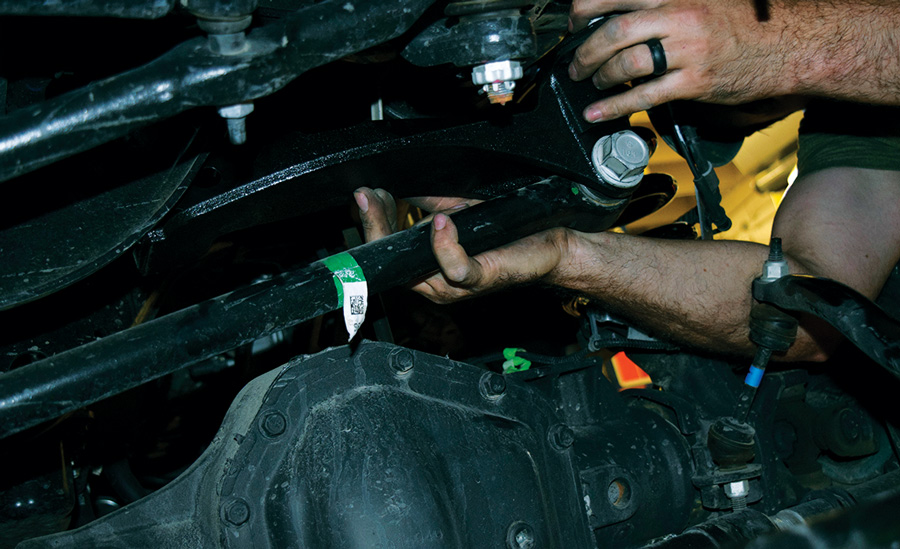
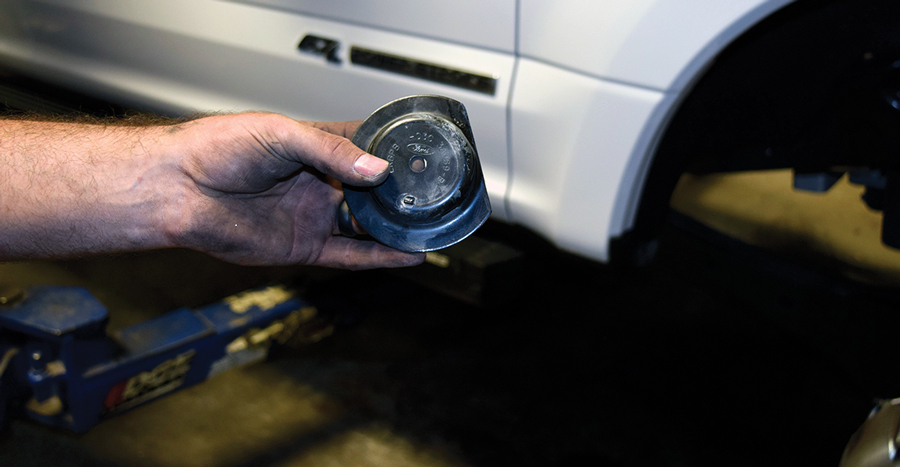
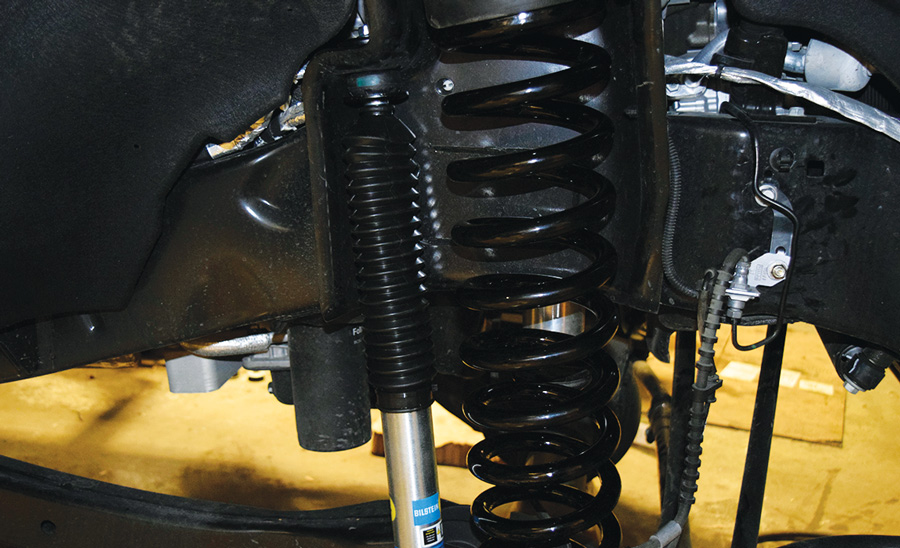
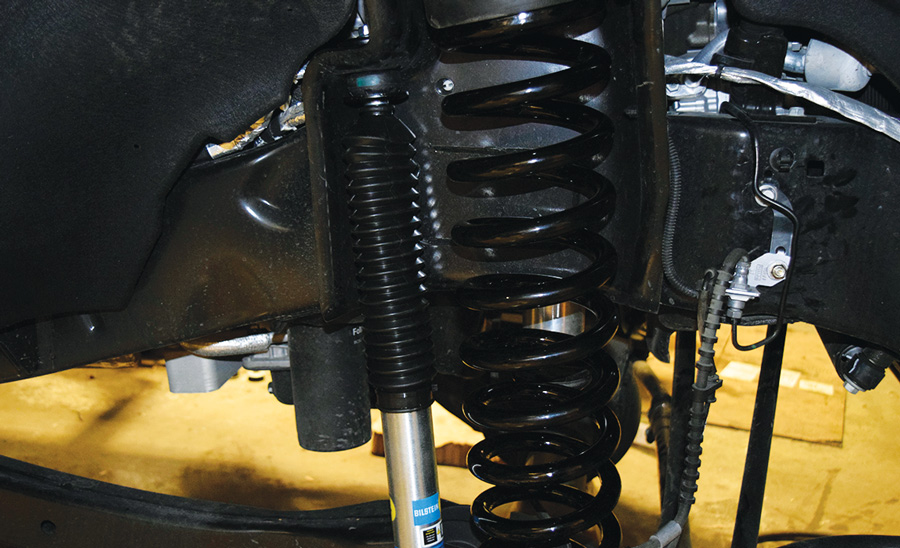
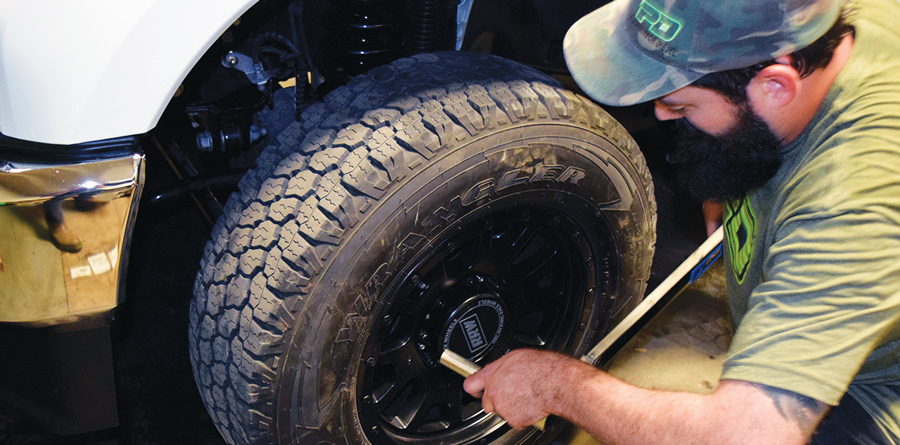


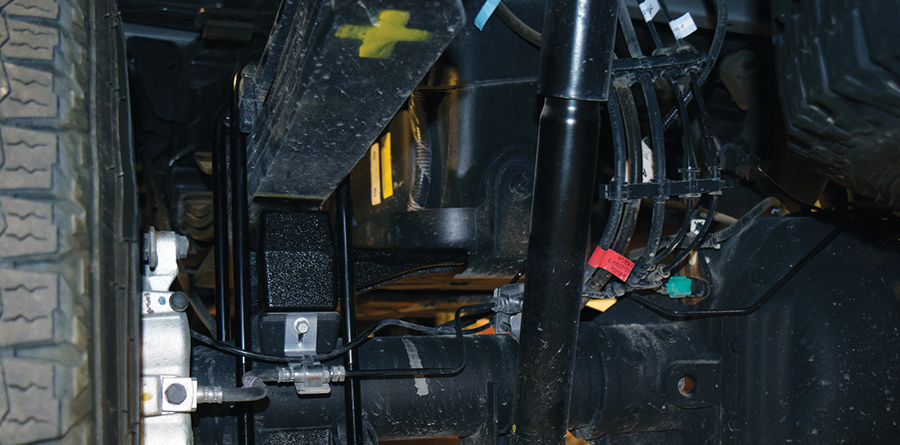
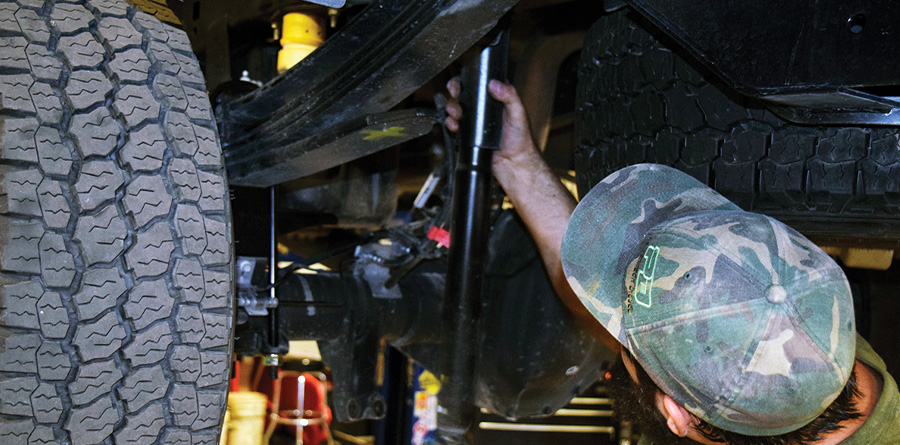
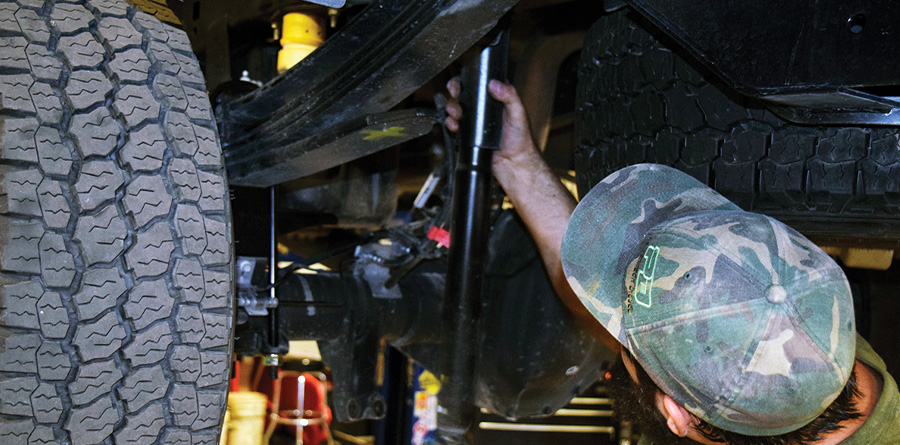

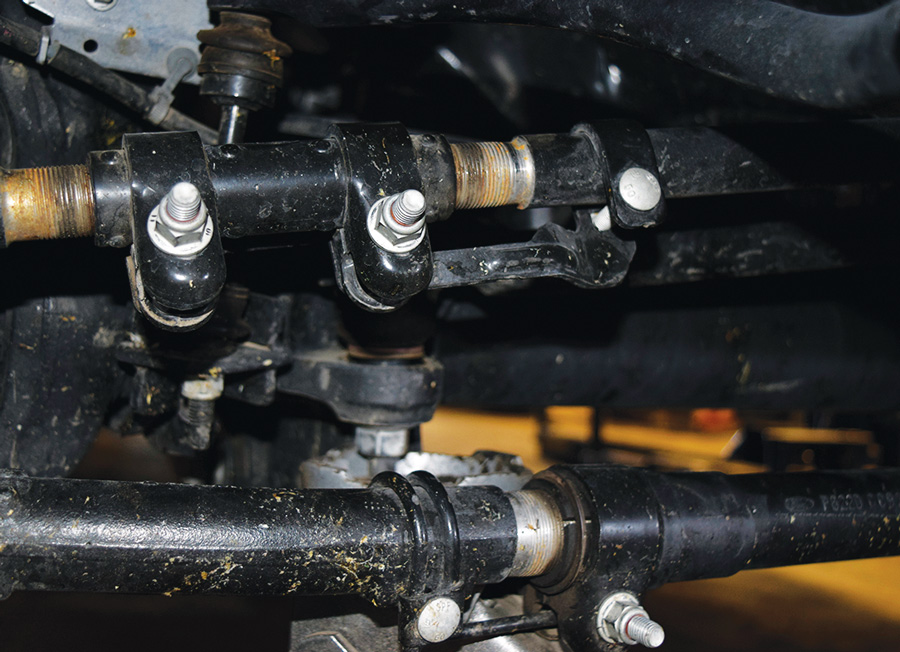
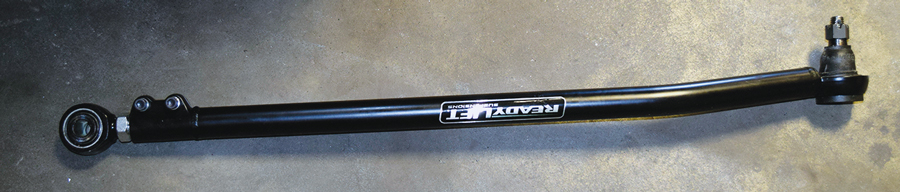
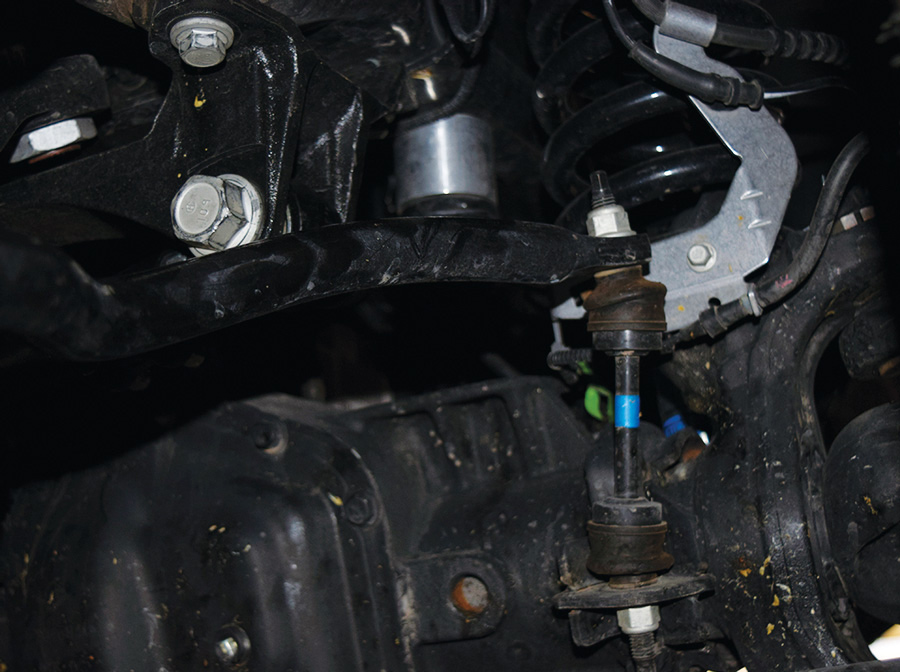
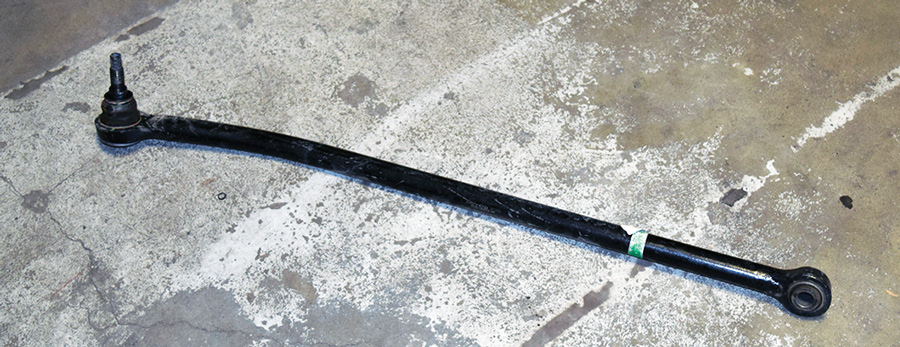
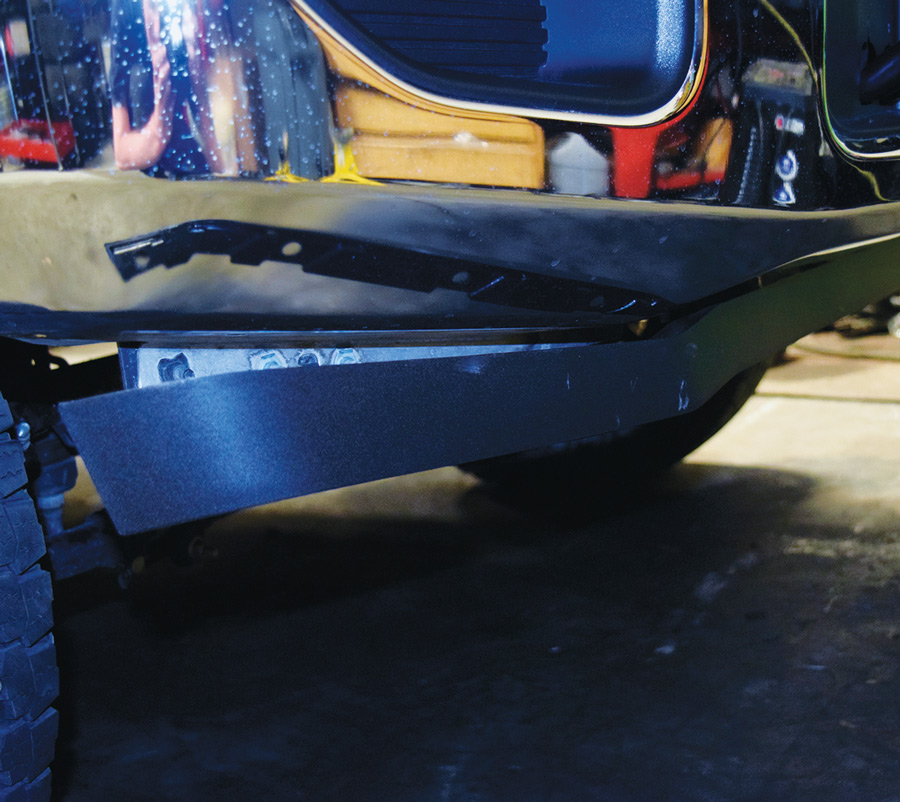
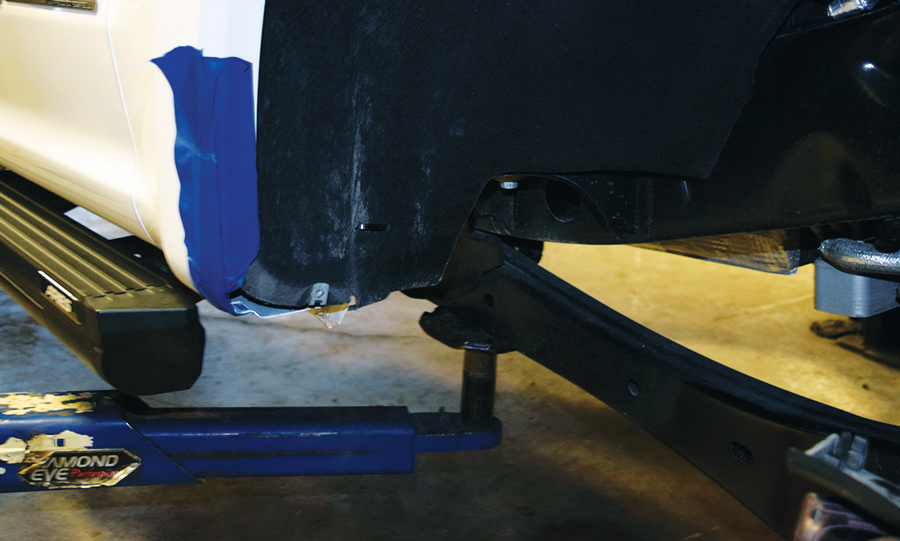
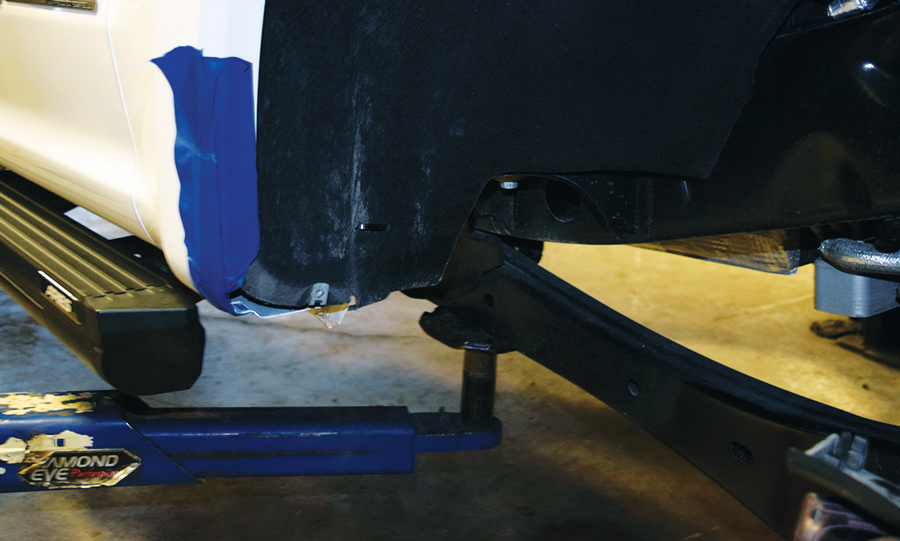

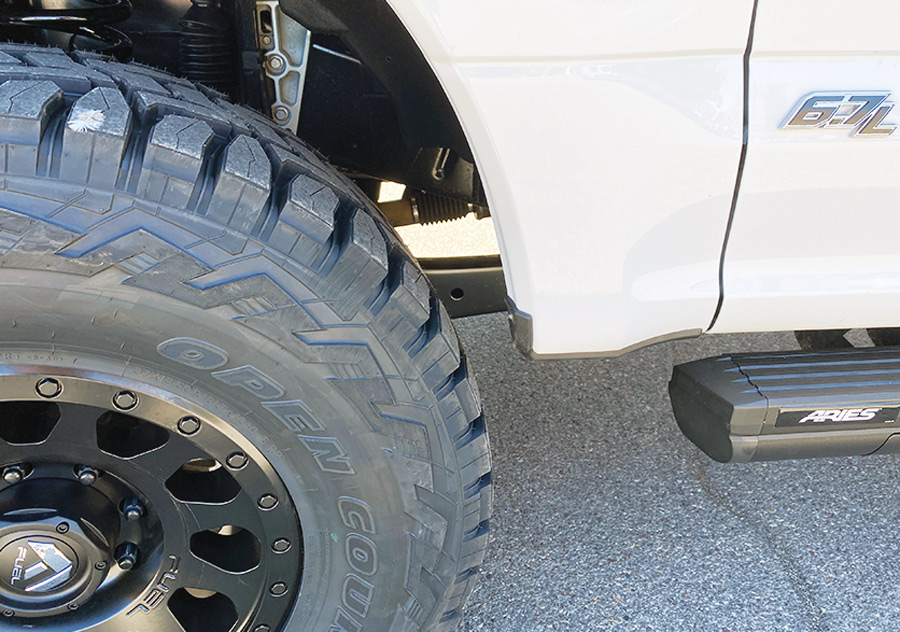
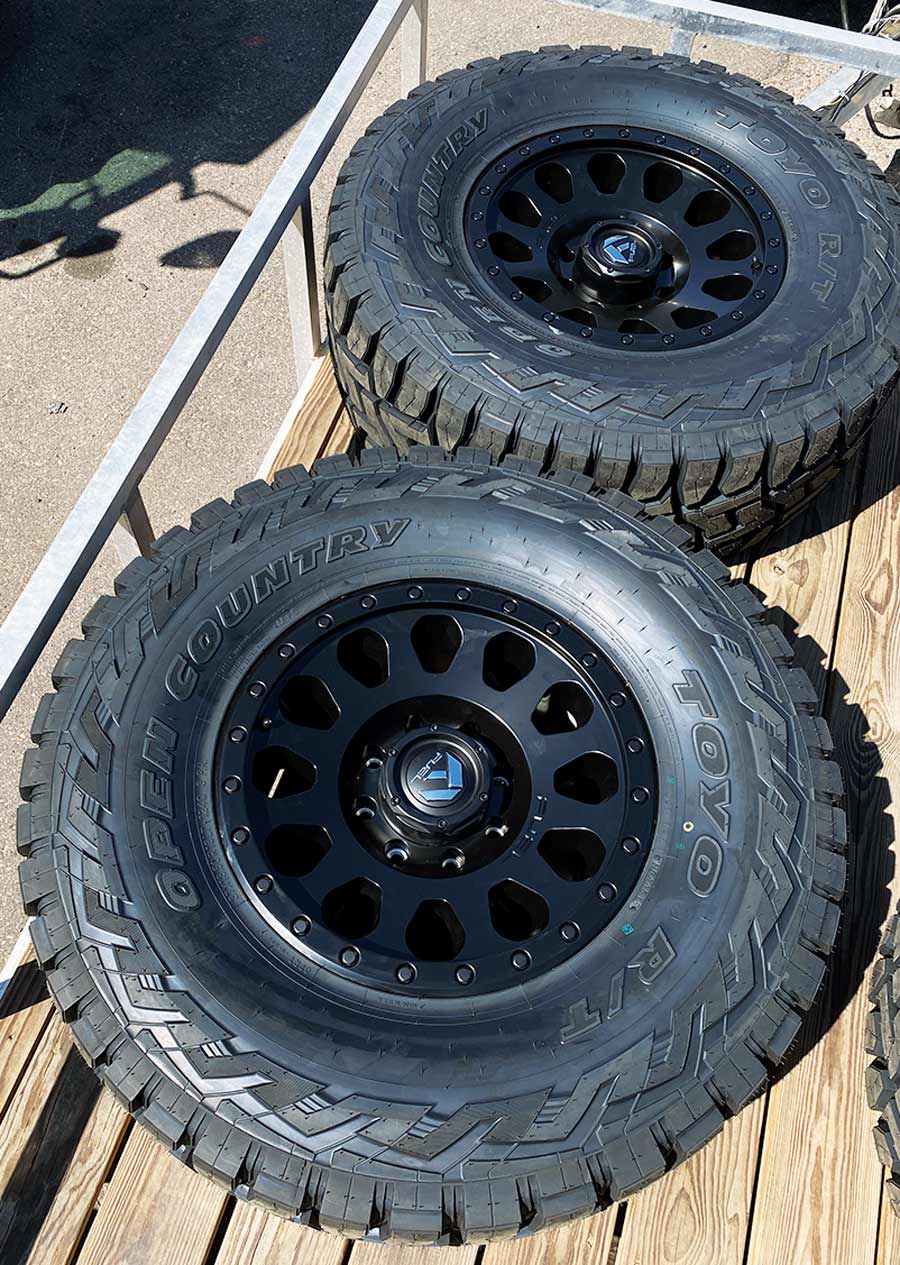

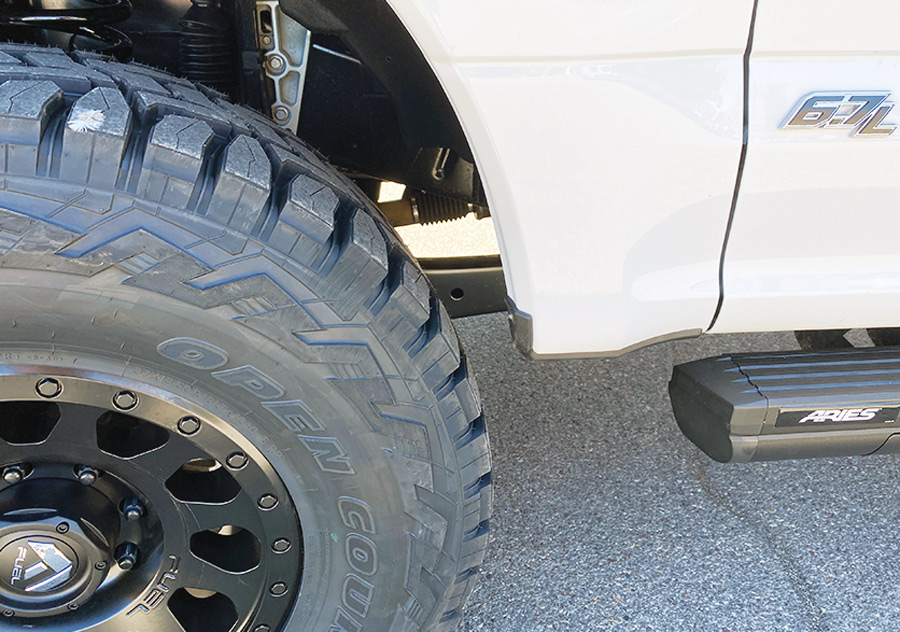
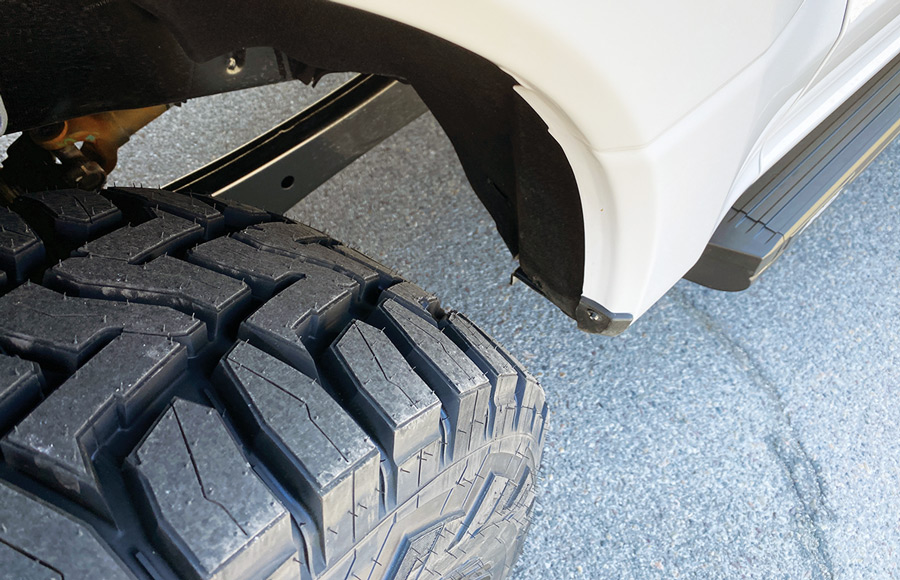